MHI Solutions - March 2015
The Rise of Automation and Robotics in Supply Chains
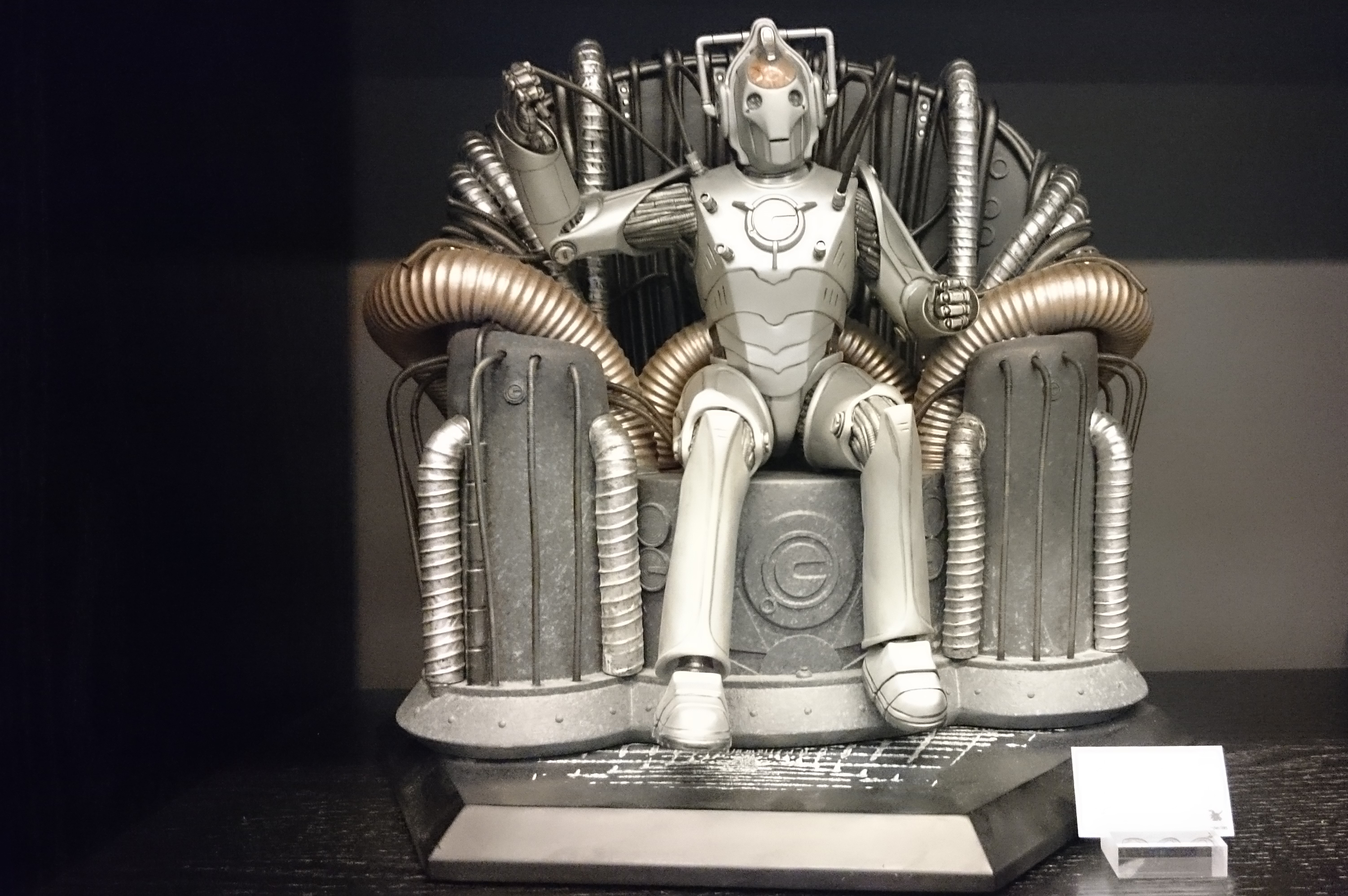
On “Star Trek: The Next Generation,” Capt. Jean-Luc Picard often pondered the week’s signature conundrum over a cup of comfort.
“Tea. Earl Gray. Hot,” he’d say to the Replicator, and a moment later it would materialize.
We’re not quite there just yet, but at this year’s Consumer Electronics Show in Las Vegas, we got one giant step closer with the debut of COOKI, the prototype for a robot that, in conjunction with an app that knows what fresh ingredients are available in your fridge, can present a list of recipes that work within those parameters and bring it all together right there in your kitchen.
“I love to cook,” says Henrik I. Christensen, Ph. D., “but I’m sure I would give it up for a machine that will do it for me. It’s very cool!”
Christensen is the KUKA chair of robotics at the College of Computing at Georgia Institute of Technology and the executive director of the Institute for Robotics and Intelligent Machines. He collaborates with the likes of Apple, BMW, Electrolux and tens of others. “Very cool” is a pretty stellar review.
It might be a decade or more before COOKI’s robotic arm is whipping up a staff lunch in your warehouse’s break room, but her bigger, burlier cousins will likely be out on its floor well before then. Robotics and automation is moving forward at veritable light speed, and the laws and regulations governing their use is finally catching up to the technology.
In 2015, say the experts, robots will not only be streamlining the process and facilities of the supply chain, they’ll be working right alongside their human co-workers (and keep right on going when everyone else heads home for dinner).
Robots as job creators?
“At the end of the day,” says Christensen, “people want to have more agility in their supply chain, to send materials with very little storage, very rapid reaction, very high speed.”
Robotics, he says, is about empowering people to do just that. Though some workers are wary that automation will do away with their jobs, Christensen says more often than not, robots merely shift employees to other positions. Generally, better ones.
“The automotive industry did not buy robots to replace people, they did it to get consistent quality, which allowed them to grow.”
“Robots enhance the workplace,’ says Scott Melton, regional manager of FANUC America West. “And robotics takes people out of hazardous environments – places where they are palletizing, loading them onto ATVs. It eliminates strenuous jobs where the risk of injury, whether immediate or over time due to repetition, is very high.”
Jobs that both he and Christensen say most people don’t want to do, anyway.
“High turnover is one of the supply chain’s biggest challenges,” Christensen points out. “The good news is that when we install a robot, it will work 24/7 and it could be 10 years before you have to do anything for it.”
Helping companies produce and/or deliver goods faster, says Melton, allows them to be competitive and grow. He cites FANUC client Noble Plastics, a Louisiana-based operation that has continued to expand – and hire – as they’ve implemented robotic automation. FANUC also helps Noble train employees to work in the new environment.
“We may take an actual welder off the welding,” says Melton, “but because he or she is an experienced welder, they have the knowledge of operation. Who better to train to run the robot than the people who know how the robot should best function? And most of the companies we work with choose to invest in the training.”
In fact, many contribute to the automation enhancements well before the robots begin their tenure.
“Those who work on the shop floor are often involved in the full process of designing and creating the logistical solutions,” says Tom Pollard, applications engineer for RMT Robotics, Ltd. “You want those people to be onboard, and they can learn a lot through the process of implementing the technology that will help them to operate it smoothly when the time comes.”
And, Melton points out, it gives them new and valuable resume add-ons. “Operating, programming and maintaining robots is a skill set that is desperately needed throughout the U.S.”
Tearing down barriers
Innovations in robotics – and the laws that govern its use – are now allowing machines to work side-by-side with their “human overlords.”
In the past, safety barriers and sensors prohibited people from working too near the machines – creating a timely process if someone noticed, for example, that a package was upside-down: Shut down machine. Open barrier. Right package. Close barrier. Power on. Work resumes.
“We’ve developed technology that allows the robot to sense the proximity of the person working near it and act accordingly,” says Melton, “whether than means it moves slower or stop completely – until its work zone is clear.”
Indeed, says Christensen, this new generation of robots is safe to use around humans. “And there is now a standard for collaborative robots that defines the safety mechanisms necessary to make sure no one gets hurt when they are sharing the same space.”
The technology has been around for quite a few years, “but it was not until more recently that we had the legal framework allowing companies to deploy them. Now OSHA and others can approve facilities where robots and humans can work side-by-side.”
In all of the above examples, notes Christensen, “we not only streamline the process, but the traffic, as robots can run in much smaller aisles.” This, he says, translates to a warehouse that’s smaller overall. “Robots can typically decrease the environmental footprint of a facility.”
Productivity up
With no worry about the wear-and-tear that plagues us carbon-based life forms, robots can in many cases outperform the most efficient human in your warehouse by an astonishing percentage.
“The trend is towards goods-to-person order fulfillment,” says Pollard, who acknowledges that as the skew requirements in the warehouse go up, human workers are getting less efficient. “It’s pretty difficult for a worker to pick from a warehouse that might have 20,000 items in it.”
Before, says Christensen, a good worker might be able to do 60 picks an hour. “With a robot you can increase your efficiency to something like 360 picks. And at the same time, you’re taking away a lot of the heavy physical labor.
Individualized picking – Christensen uses the example of toothbrushes to the local supermarket – essentially turns humans into biological robots controlled by voice command, workers scrambling about warehouses to pull 20 of Brand X, 20 of Brand Y, and so forth, since these markets can’t store a glut of any one product. The introduction of automation here, he says, will not only eliminate much of the lifting and repetition, but reduce costs, as well.
“Today you have to place items where they are reachable by humans – say, one foot off the floor up to perhaps six feet above it,” he explains. With robot assistance, the storage space is astronomically condensable. “The robots now bring the items the workers. All they have to do is package it.”
And the items these machines can pull, says Melton, are about to become as varied as any given customer’s order from Amazon.
“We’re going to see robots with vision,” he says. “3D vision for bin picking, for handling mixed products, a technology that allows you to sort product by size, allowing mixed products to come into the robot zone.” The applications allow robots to scan an item – using a combination of cameras and lasers – and recognize it, for example, as a box that measures 20 x 20 x 20 versus a 10 x 10 envelope that’s a quarter-inch thick.
“This allows product to come in randomly or as needed,” says Melton. “So whether it might be loading different metallic parts that need to be delivered or working in a distribution warehouse, where there are differently sized packages, boxes or containers, 3D vision is going to be driving the technology and open up a whole bunch of applications that didn’t exist in the past.”
And once you can dimensionalize, says Pollard, you can do a lot of other things.
“One of the problems with manual picking is that it’s unpredictable,” he explains. “Say you have to ship 5,000 containers of different sizes on a truck across the country. Hand that order to the workers and one will turn it into 25 pallets, another worker will do it in 30, another in 10.”
Though each might be doing his or her job very well, you can’t schedule the truck or check the weights – you can’t do any of it ahead of time. Planning the physical logistics of loading must wait until the workers are through.
“But, if you can accurately measure the product, using software that can determine the way in which those products need to go on the pallet to create a stable load, along with the automation to place it there, you can plan all the logistics before it happens and optimize it,” says Pollard. And such technology does exist.
Expensive? That depends on your budget. But semi-automatic options can be more cost-effective and perhaps, Pollard notes, even better solutions.
For example, products could be provided to the worker in a goods-to-person order-picking scenario, who then allows the program to show ways in which it might be loaded on the pallet. He or she can either go with the suggestion or employ another idea that would make it even more stable or dense.
“You’re blending the skills of the worker with that of the automation for a solution that turns out to be better than either could do on their own.”
Hands-free warehouse work notwithstanding, it’s hands-free driving that could end up being the supply chain innovation of the new millennium. Christensen said GM higher-ups are predicting that driverless trucks will be doing much of the transport by 2020.
Massive infrastructure upgrades notwithstanding, he himself predicts that children born today will never drive a car.
He’s not as quick to give up driving, however, as he is cooking.
“I love my car,” he says, chuckling. “They’re going to have to drag me out of it. But for the rest of the world, I’m sure it will be very nice.”
Photo courtesy of Amy Drew Thompson (Author)